مدلسازی و شبیه سازی خط تولید عملیات خشک کردن پودر PVC:
مطالعات تجربی و تئوری سینتیک خشک کردن در مقیاس ذرات* (بخش اول)
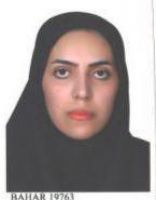
کاملاً واضح است که خشک کردن PVC توسط رقابت بین انتقال داخلی و خارجی انجام میشود. سینتیک خشک کردن با استفاده از مدل شبیه سازی کوچک شدن هسته و رسیدن به یک حالت پایدار یک بعدی در یک خشک کن پنوماتیک مورد بررسی قرار گرفت. یک مدل دوفازی پیوسته برای توصیف جریان حالت پایدار استفاده گردید، در خشک کن فاز پراکنده رقیق (پودر PVC مرطوب) و فاز پیوسته (هوای مرطوب) بود. در این مدل انتقال حرارت هم رفتی، انتقال جرم و انتقال حرکت در نظر گرفته شده است. نتایج عددی با داده های تجربی بدست آمده از صنعت مورد مقایسه قرار گرفتند. نتایج نشان می دهند که دمای ورودی، مهمترین پارامتر در این عملیات است.
مقدمه
این تحقیق در آزمایشگاه مهندسی شیمی در تولز به همراهی INEOS ChlorVinyls صورت گرفته است. در خط تولید پودر PVC، پس از مرحله پلیمریزاسیون، سوسپانسیونی متشکل از آب و ذرات PVC، بدست میآید. مقدار زیادی از آب این سوسپانسیون در مرحله سانتریفیوژ حذف میشود، و پودری متخلخل به نام کیک (با رطوبتی بین 2/0 و 35/0 کیلوگرم آب بر کیلوگرم PVC خشک) بدست میآید. خشککردن کیک اساساً در یک خشککن پنوماتیک همراه با یک بستر سیال که نقش از بینبرنده باقیمانده رطوبت PVC (کمتر از 05/0 کیلوگرم آب بر کیلوگرم PVCخشک) را دارد، رخ میدهد. در مجموع برای انجام این عملیات انرژی زیادی در حدود 800 تا 1500 صرف میشود، شرایط عملیاتی و گرید PVC نشاندهنده 30درصد از هزینههای تولید میباشد. برای کاهش قیمت خشککردن پودر PVC، مهمترین قدم، درک پدیدههای فیزیکی مختلف درگیر در این امر (پدیده انتقال جرم، انتقال حرارت، پدیدههای هیدرودینامیکی خاص خشککردن) میباشد. تمرکز این تحقیق ابتدا بر روی به دستآوردن دادههای سینتیکی در یک بستر سیال متراکم و در مرحله دوم روی مدلسازی فرآیند هیدروژنزدایی از ذرات PVC در یک خشککن پنوماتیک است.
سینتیک خشککردن با استفاده از غوطهوری میزان کمی ذرات PVC (قطر=143پیکومتر) در بستر یک سیال گرم پرشده با مهرههای شیشهای (قطر=324پیکومتر) بدست آمد. نقش این ذرات بزرگتر جلوگیری از پدیده تراکم بین ذرات PVC و خشکشدن این ذرات در شرایط ایزوترمال است. نتایج تجربی نشان میدهند که سینتیک خشککردن به شدت به دمای هوا و رطوبت وابسته است.
این نتایج تجربی با توجه به مدل سینتیک برپایه تبادل حرارت و جرم بین PVC و هوا (انتقال خارجی) و نفوذ گرما و جرم داخل ذرات (انتقال داخلی) ارائه شدند. آن مدل سینتیک شامل یک خشککن پنوماتیک تکبعدی در حالت پایدار است که با استفاده از خشکهای صنعتی شبیهسازی شده است.
2. پیش زمینه
خشککردن محیط متخلخل یک مشکل پیچیده است و هنوز هم با توجه به مطالعات گستردهای که در این زمینه صورت گرفته و با توجه به مبادلات صورت گرفته (جرم، گرما و انتقال سرعت) بین گاز و ذرات، همچنین پارامترهای وابسته به مورفولوژی ذرات جامد و تمایل آب/جامد، به خوبی درک نشده است. چنانچه در شکل 1 نشان داده شده است، دو مرحله در فرآیند خشککردن ذرات متخلخل کاملا مشهود است. مرحله اول شامل حذف آب آزاد جمعشده در سطح میباشد. در این مرحله تبخیر توسط فرآیند انتقال خارجی کنترل میشود که این انتقال طبق تکنولوژی دستگاه خشککن میتواند از نوع همرفتی، هدایت یا تابش باشد. در تحقیق ما (خشککن پنوماتیک با بستر سیال)، این انتقالات از نوع همرفتی است و بستگی به سرعت موضعی بین هوا و ذرات دارد و به نام سرعت لغزشی نامیده میشود. این انتقالات که به نوع تکنولوژی خشککردن بستگی دارد به طور گسترده مورد مطالعه قرار گرفته است، در برخی از اوقات یافتهها دارای همبستگیهای فراوانی بوده اما گاهی نیز بین آنها تناقضاتی دیده میشود.
در مرحله دوم، آب موجود در خلل و فرج ذرات حذف شده است و فرآیند خشککردن به وسیله ترکیبی از دو انتقال داخلی و خارجی کنترل میشود. انتقال داخلی به خواص و ساختار ذرات جامد بستگی دارد. مطالعات نشان میدهند که ممکن است در طول فرآیند خشککردن بسیاری از پدیدههای ابتدایی رخ دهد. برخی از این پدیدهها پیچیده هستند و به ساختار ذرات جامد بستگی دارند، مانند ارتباط بین آبـجامد، و ترکیبات آب. این مکانیسمهای ابتدایی در شکل 2 قابل مشاهده است.
- نیروهای کاپیلاری، به ترشوندگی سطح ذرات جامد توسط مایع
، دمای مایع و سایز ذرات خالص و توزیع آنها وابسته هستند. این خواص روی فشار اشباع بخار آب در سطح مشترک مایع/جامد و حرکت ذرات مایع در خلل و فرج تاثیر میگذارند.
- نفوذ بخار از طریق خلل و فرج تحتتاثیر درجه حرارت و فشارجزئی بخار آب است.
- نفوذ جامد متناسب با مهاجرت آب موجود در سطح جامد است. این مکانیسم خصوصاً در مواردی رخ میدهد که جامد در آب حل میشود و پیوندی بین آب و جامد تشکیل میشود (واکنش شیمیایی، پیوند هیدروژنی و ...).
بنابراین نظریه مدلسازی خشک¬کردن ذرات تر به وسیله هوای داغ بدین صورت ارائه می¬شود:
تبخیر آب در سطح ذرات در طول زمان خشک شدن در سرعت ثابت، و بین دو منطقه هسته تر و پوسته خشک ذرات صورت می¬گیرد. این منطقه عملیاتی از سطح ذرات تا هسته آنها را شامل می¬شود. با استفاده از شبیه¬سازیهای متعددی که روی مواد متخلل گوناگون، انجام شده است، ضخامت منطقه¬ای که باید تحت عملیات خشک¬کردن قرار گیرد به خواص ترکنندگی مایع در منافذ بستگی دارد: اگر ترکنندگی کامل باشد، مایع می¬تواند وارد سطح داخلی منافذ شده و روی شیب حرارتی تاثیر بگذارد.
در تحقیق پیش¬رو، خواص ترکنندگی PVC، به تنش سطحی (γ_LV ) محلول مایع مورد استفاده در طول مراحل پلیمریزاسیون و همچنین تمایل بین ذرات جامد و این محلول که با نام زاویه تماس (θ) شناخته می-شود، بستگی دارد. میزان کم تنش سطحی و بالابودن زاویه تماس (بین (°80 تا °94.7) ما را به این فرض نزدیک می¬کند که عملیات خشک¬شدن می¬تواند نتیجه ناپیوستگی سطحی باشد.
با توجه به اثر کاپیلاری، توزیع سایز ذره خالص ذرات PVC، که در شکل 3 آورده شده است، نشان می¬دهد حداقل سایز ذرات حدود nm30 می¬باشد. قانون کلوین بیان می¬کند که فعالیت آب (°pw/p ) به عنوان ضریبی برای شعاع حفره به کار می¬رود، و نشان می¬دهد که برای شعاع حفره بزرگتر از nm10، فعالیت آب برابر یک است. از این رو، در این مطالعه اثر کاپیلاری تعادل آب/مایع را تحت تاثیر قرار نمی¬دهد.
با توجه به نفوذ جامد و مایع، طبق نتایجی که در مطالعه قبلی INEOE's روی PVC صورت گرفته بود، مشاهده شد که PVC نامحلول در آب بوده و دارای میل ترکیبی پایینی با آن می¬باشد. به عنوان مثال، در اتمسفری با رطوبت نسبی 75% رطوبت تعادلی PVC برابر 4/2 گرم در آب/کیلوگرم PVC خشک، می¬باشد (در ℃50). از این رو، می¬توان نفوذ مایع و جامد را در این مطالعه نادیده گرفت و تنها انتقال داخلی باقی-مانده، نفوذ بخار آب می¬باشد. شیب این مکانیزم توسط درجه حرارت و فشارجزئی بخارآب تحت تاثیر قرار می¬گیرد.
در شکل 4 تصاویر SEM ذرات PVC مشاهده میشود، یک ساختار صفحهای معمولی در تصویر مشاهاده میشود که هر ذره یک توده از ذره اولیه است. با چنین ساختاری دو خانواده از حفرات را میتوان متمایز کرد:
- فاصله بین ذرات اولیه (اندازه منفذ nm250) که ماکرو متخلخل هستند (میانگین سایز منافذ /6nm3335) است. این منافذ توسط خشککن پنوماتیک خشک شده است (93% حجم منافذ).
تخلخل موجود در ذرات اولیه (اندازه منفذ کمتر از nm250) که مزومتخلخل هستند (میانگین سایز این منافذ nm81/6 است) این منافذ در خشک کن با بستر سیال خشک شده است (7% از حجم منافذ).
در مطالعاتی که توسط محققین متعدد انجام شده، از مدل کاهش هسته استفاده شده که برای نشان دادن فرآیند تبخیر در ذرات دارای ساختار صفحه¬ای ـ دانه¬ای استفاده گردیده است. در این مدل، ذرات به دو ناحیه تقسیم می¬شوند: یکی هسته مرطوب، که هر لحظه در حال کاهش است و دیگری پوسته خشک، که از طریق آن آب تبخیر شده به سطح ذرات پخش می¬شود. اولین مکانیسمی که در این مرحله مشاهده می¬شود، انتقال گرما به روش هدایتی (از سطح ذره به هسته) و انتشار بخارآب از طریق خلل و فرج است. اگر انتقال گرما منجر به پدیده خشک¬شدن گردد، مشکلی قابل مقایسه با مشکل کلاسیک استفان در تبخیر یا انجماد قطرات ایجاد می¬گردد. { 17و 18
در خصوص خشک¬کن پنوماتیک باید به این نکته توجه داشت که استفاده از تکنولوژی این خشک¬کن¬ها در مواردی است که در سیستم آب اضافی یا آبی محصور شده، وجود داشته باشد. یک خشک¬کن پنوماتیک یک خشک¬کن پیوسته با انتقال همرفتی و انتقال جامد رقیق است. این تکنولوژی دارای مزایای متعددی مانند:
زمان اقامت کوتاه ذرات؛ که خشک¬کن مجاز به استفاده برای مواد حساس به گرما می¬شود،
در جریان موازی، درجه حرارت بالا را می¬توان در ورودی اعمال کرد، و در نتیجه در درجه حرارت¬های بالا کارکرد دستگاه بهینه است،
از خشک¬کن می¬توان به عنوان سیستم انتقال استفاده کرد، می¬باشد.
از دیدگاه هیدرودینامیکی، خشک¬کردن پنوماتیک مشابه انتقال پنوماتیک است. از این رو، در ادامه چندین مدل انتقال پنوماتیک مورد بررسی قرار می¬گیرند. در این مدلها، برهمکنش (جرم، گرما و انتقال حرکت) بین یک فاز گازی و یک فاز پراکنده همراه با مکانیسم¬های داخلی در نظر گرفته می¬شود.
3. مواد و روشها
آزمایشات تجربی با استفاده از کیکی که توسط موسسهINEOS کلرووینیل فرانسه (مشخصات آن در جدول 1 آورده شده است) سنتز شد، انجام شد. آنالیز اندازه ذرات یک توزیع گوسی را با قطر اصلی μm144 نشان می¬دادند. مشخصات ذرات در جدول1توسط لیزر گرانومتری (Malvern Mastersizer 2000-Sirocco 2000- ±0.1μm) اندازه¬گیری شد. دانسیته ذرات، تخلخل، پیچ¬خوردگی و توزیع سایز ذرات خالص (شکل 3) به وسیله یک تخلخل¬سنج جیوه¬ای روی محصول خشک محاسبه گردید. برای اندازه¬گیری رطوبت کیک، نمونه-های مختلفی تهیه شد و در یک آون تهویه¬دار در 50 درجه سانتی¬گراد در طول 24 ساعت قرار گرفت. رطوبت اولیه کیک بین 195/0 و 205/0 کیلوگرم آب بر کیلوگرم PVC خشک بود.
نتایج اولیه نشان دادند که سینتیک خشک کردن در یک خشک کن همرفتی قویاً وابسته به شرایط خارجی است (وزن نمونه و ضخامت، نرخ جریان هوا و...). برای بررسی این مطلب، مطالعه بر روی پدیده¬های فیزیکی در سایز ذرات بسیار مشکل است. به همین دلیل، بررسی¬های مختلفی در آزمایشگاه ما صورت گرفت، سینتیک خشک¬کردن، به وسیله فروبردن یک نمونه کوچک از PVC مرطوب (حدود g3) در یک سیال با بستر داغ که شامل 3/1 کیلوگرم مهره¬های شیشه¬ای با قطر اصلی ذرات در حدود m μ 324 بود، مورد مطالعه قرار گرفت (برای مشاهده مشخصات جدول 1 را ببینید).
در شکل 5 راهنمای آزمایشات تجربی ارائه گردیده است. یک خشک¬کن شامل یک شیشه استوانه¬ای با قطر cm10 و ارتفاع cm40 می¬باشد. وجود یک بخش طولانی در بالای آن مانع از حضور ذرات ریز در محصول می-شود. هوای مایع در یک هیتر الکتریکی گرم شده، و در هنگام نیاز با بخار آب تولیدشده به وسیله بخارسازی که در شکل 4 نشان داده شده است، مخلوط می¬شود. جریان آب به وسیله یک هیتر الکتریکی گسترش می-یابد. آب بلافاصله به بخار تبدیل شده و وارد جریان هوای گرم می¬شود. سرعت جریان مایع¬شدن متناسب با سرعت انتخابی (حداقل مایع سازی و تنظیمات سرعت نهایی) ذرات PVC و مهره¬های شیشه¬ای می¬باشد. این مقادیر که در دمای محیط اندازه¬گیری شده¬اند، در جدول 1 ارائه شده است. سرعت جریان هوا از رنج 25 تا cm/s 40 انتخاب شده است، که با حداقل سرعت مایع¬شدن دانه¬های شیشه¬ای متناسب است.
خشک¬کن به چندین سنسور دمایی (℃1/0±) و فشاری ( 1/0bar± ) و همچنین دو خازن رطوبتی (سنسورهای دمایی و رطوبتی) مجهز شده است. چنانچه در شکل 4 نشان داده شده است یک پمپ خلاء برای اندازه¬گیری رطوبت هوای مرطوب تعبیه شده است. سیستم اندازه¬گیری که نقش آن اطمینان از مقدار رطوبت در شرایط ثابت است (نرخ جریان هوا و دما)، مجهز شده با یک فیلتر برای جلوگیری از حضور ذرات برای صدمه زدن به سنسورها می¬باشد، یک حمام ترموستات برای ثابت نگه داشتن دما و جلوگیری از تراکم پدیده-ها، رطوبت¬سنج hygrometer، و یک روتامتر برای ثابت¬ نگه¬داشتن سرعت جریان هوا می¬باشد. این رطوبت¬سنج نقطه شبنم هوا را با درستی ℃1/0 اندازه¬گیری می¬کند. این رطوبت¬سنج به وسیله یک رطوبت¬سنج ثانویه که در مسیر خروجی قرار دارد، کنترل می¬شود (اندازه¬گیری رطوبت¬نسبی با درستی 1/0% است). برای ممانعت از تراکم در نزدیکی سنسورها، لوله با استفاده از کابلهای حرارتی گرم می¬شود. هر دو رطوبت¬سنجها به سیستم جمع¬آوری داده¬ها که مجاز به ثبت رطوبت هوا در مقاطع مختلف زمانی هستند، مجهزند.
در مطالعات گذشته که بر روی رطوبت¬سنج¬ها متمرکز شده بود، نشان داد که زمان پاسخ سنسورها، به زمان کارکرد آنها بستگی ندارد. زمان پاسخ برای یک مرحله سیگنال مرطوب (یعنی انتقال از اتمسفر هوای خشک به اتمسفر هوای مرطوب) حدود 40 ثانیه می¬باشد، در حالی که این زمان برای سیال در حدود 1 دقیقه است (شکل6). این مطالعه نشان داد که با هر دو نوع رطوبت¬سنج می¬توان تغییر از اتمسفر هوای خشک به اتمسفر هوای مرطوب (دمای اتاق) را اندازه¬گیری کرد، در این رطوبت¬سنجها برای انتقال رطوبت دریچه¬هایی در سیستم تعبیه شده تا در صورت نقص ناگهانی سنسورها در نمونه از آنها استفاده گردد. پاسخ سنسور با استفاده از یک راکتور با جریان برق (نشان دهنده ی تاخیر در طول اولین ثانیه از آزمایش)، و یک راکتور ناپیوسته با زمان ثابت 9/5 ثانیه (شکل5)، مدل¬سازی شد. پاسخ¬های تجربی و عددی بدست آمده از رطوبت-سنج در یک مرحله از اندازه¬گیری رطوبت در شکل 5 ارائه شده است. مدل تابع انتقال رفتار رطوبت¬سنج، برای بررسی و مدل¬سازی نتایج سنیتیک مورد استفاده قرار می¬گیرد. بنابراین برای تشخیص سنیتیک تجربی، استفاده از نتایج خام سنتیک ذاتی بسیار مهم است: سنتیک واقعی خشک کردن در بستر سیال.
محدوده دمایی از 30 تا ℃60 انتخاب گردید: اگر دمای سیال بیش از ℃ 70 باشد سطح PVC شروع به چسبنده شدن کرده و موجب اگلومریشن در سیال میشود. طبق مطالعات رطوبت نسبی هوای اطراف بین 1/2 تا 1% /63 در نظر گرفته شد.
4. روشها
تغییرات زمانی در رطوبت نسبی هوای خروجی (RH) در طول هر آزمایش ثبت گردید، این تغییرات برای محاسبه هر Y که رطوبت مطلق هوا (در هر کیلوگرم آب/کیلوگرم هوای خشک) می¬باشد، موردنیاز است؛ همچنین Wdrying، نرخ جریان هوای خشک (هر گرم آب/ثانیه) است که برای محاسبه میزان جریان هوای خشک که از خشک کن بدست آمد، موردنیاز بود:
Th دمای اندازه گیری شده به وسیله رطوبت سنج (در ℃)، p0Th فشار بخار استاندارد آب در این دما، و P فشار مطلق در خشک کن بود.
با رسم منحنی تغییرات زمانی جریان هوای خشک کن، مقدار آب بخارشده در طول زمان t (mw) و مقدار کل بخارآب (mw0) در طول آزمایش بدست آمد. این اطلاعات محققان را قادر به محاسبه (X0) رطوبت جامد اولیه و (X) رطوبت جامد (به همراه m0 به عنوان وزن نمونه خشک) ساخت:
رطوبت اولیه محاسبه شده مربوط به رطوبت اولیه اندازهگیری شده در آون تهویه دار در ℃ 50 و در مدت 24 ساعت با خطای اندازه گیری کمتر از 5% میباشد. تغییرات زمانی رطوبت جامد نرمال (X/X0) در شکل 7 ارائه شده است، از این اطلاعات برای بدست آوردن زمانهای t75، t50، t25 و زمان خشک شدن، یعنی زمانهای لازم برای رسیدن به رطوبت جامد نرمال به ترتیب 0/75، 0/50، 0/25 و 0/05 استفاده میشود.
5. نتایج اولیه
کیک (PVC مرطوب) یک پودر بسیار منسجم است، بنابراین ذارت تمایل به اگلوموریت شدن (کلوخه) دارند. این پدیده سبب کاهش انتقالات داخلی و خارجی میگردد. به علاوه، ذرات بزرگتر انتقال همرفتی پایینتری دارند. به همان روش، انتقال داخلی در ذرات اگلومریت شده مانند بخار آب کاهش یافته و دارای مسیر نفوذ طولانیتر میباشد. پس میزان هوای خروجی مرطوب در طول مسیر خشک کردن با نمونه کیک در جرمهای مختلف ارزیابی گردید. رطوبت محاسبه شده اولیه با رطوبت واقعی نمونه مورد مقایسه قرار گرفت. این مطالعه نشان داد که جرم بهینه بین 2 و 4 گرم میباشد. در واقع با جرم کمتر دقت حسگر بیش
از حد کم است و با جرم بیشتر به دلیل چسبندگی ذرات به یکدیگر و لزوم جداسازی آنها، نتایج قابل تکرار نخواهد بود. بنابراین برای کاهش این پدیده ها، نمونه با دانه های شیشه ای در دمای محیط قبل از وارد کردن به بستر سیال، مخلوط میشود. در شکل 8 نشان میدهد، نسبت جرمی 25% دانههای شیشه ای دارای نفوذ بالاتری است. برای مقادیر بالاتر، زمان خشک کردن ثابت باقی می ماند. از این رو، آزمایش های زیر با استفاده از 30% نسبت جرمی دانه های شیشها ی انجام شد.
شکل b و a9 یک نمونه از نتایج بدست آمده با شرایط آزمایشگاهی که در جدول 2 لیست شده را نشان میدهد (آزمایش 1).
میتوان مشاهده کرد که:
- زمان خشک کردن حدود 30ثانیه، بسیار نزدیک به زمان پاسخ رطوبتسنجها است،
- یک تاخیر 3ثانیهای با توجه به تزریق نمونه و زمان موردنیاز برای رسیدن هوای مرطوب رطوبتسنج وجود دارد،
- رطوبت مطلق هوا و نرخ جریان هوای خشک یک سیر تکاملی مشابه دارند،
- کاهش دمای بستر در طول آزمایش زیر ℃1 باقی میماند که این امر نشاندهنده تاثیرات همدمایی شرایط آزمایش است.
در شکل 8 روند نرمال منحنی زمان رطوبت جامد برای آزمایشات مختلف در شرایط یکسان، نشان داده شده است (نمونههای 1، 2و3). این شکل نشان میدهد سیستم آزمایشی ما تکرارپذیر بوده و واریانس t50 کمتر از 1 ثانیه است.
* نویسنده: سمیه صلاحی (مدیر کنترل کیفیت شرکت پارس پولیکا)
برای مشاهده اخبار شرکت پارس پولیکا اینجا را کلیک کنید.
ادامه دارد...
نظرات