pvc-asso.ir
بالا بردن راندمان انرژی در فرایند اکستروژن
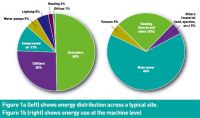
سرویس ترجمه انجمن لوله و اتصالات پی وی سی: حساسیت مصرف انرژی در فرایند تولید پلاستیک به شدت حساس بالا است. بیشتر تولید کنندگان در این صنعت هم اکنون در یافته اند که یکی از مهمترین منابع هزینه، میزان مصرف انرژی است. با وجود اینکه فرایند اکستروژن یکی از بهترین روش های تولید پلاستیک ها است، اما هنوز در بسیاری موارد امکان کاهش مصرف انرژی وجود دارد.
ابتدا قبل از اینکه شرکتی آغاز به کاهش هزینه های انرژی کند، باید بداند که هزینه ها در کجا مصرف می شوند. بهترین و دقیق ترین راه برای اینکار، نقشه برداری انرژی است تا طی آن مدلی از مصرف انرژی در هر واحد به دست آید.
برای این امر باید مدل های بصری و ریاضی انرژی به کار رود. در مدل هایی که براساس استانداردهای جهانی هستند، توزیع انرژی برای شرکت های با فرایند اکستروژن، به صورت شکل 1a است.
این شکل به صورت نمونه نشان می دهد که در یک واحد اکستروژن پروفیل، بیشترین انرژی واحد توسط بخش اکسترودرها مصرف می شود. برای سایر انواع اکستروژن مثل تولید ورق و فیلم، انرژی مصرفی خطوط پایین دستی نیز مهم است، اما همچنان مصرف انرژی اکسترودرها در راس قرار دارد.
در بیشتر واحدها، انرژی مصرفی قابل رویت معمولاً برابر انرژی مصرفی سرویس های غیر قابل رویت از قبیل چیلرها، پمپ ها، هوای فشرده و غیره است.
در خود اکسترودر نیز بهتر است مصرف انرژی جداگانه ثبت شده و بررسی شود که هر بخش چه میزان انرژی مصرف می کند. در ماشین های تولید معمولاً مصرف انرژی به صورت شکل 1b است.
شکل 1- توزیع مصرف انرژی درهر واحد تولیدی (چپ) و در هر اکسترودر(راست)
همانطور که در شکل مشخص است، در این مورد بیشترین مصرف کننده انرژی، موتور اکسترودر است که در بیشتر موارد تقریباً 66% کل انرژی ( بسته به نوع فرایند، نوع مارپیچ، چیدمان دستگاه و سایر متغیرها) مربوط به این بخش است.
این نمودارها راهنمای مفیدی برای شرکت ها هستند تا دریابند در کدام نقاط باید به فکر صرفه جویی انرژی باشند و مشخص است که اولین مورد، موتور اکسترودر است.
شکل 2- شاخص انرژی SEC واحد برای فرایند اکستروژن
شکل 3- شاخص انرژی SEC ماشین برای فرایند اکستروژن
همسویی کاهش مصرف انرژی و افزایش سرعت تولید
رایج ترین شاخص انرژی که در پروژه های کاهش انرژی کارخانه ها به کار می رود، مصرف ویژه انرژی SEC (Specific Energy Consumption) است و براساس Kwh/Kg در واحدها به کار می رود.
نتایج به دست آمده برای SEC واحدهای تولیدی دارای فرایند اکستروژن بر حسب نرخ تولید در شکل 2 نشان داده شده است و برای ماشین های تولید به طور جداگانه نیز این شاخص در شکل 3 بررسی و نشان داده شده است. هر دو شکل 2 و 3 نشان می دهند که با افزایش میزان نرخ تولید، میزان مصرف انرژی کاهش می یابد و (SEC(KWh/Kg نیز کاهش می یابد.
نکته جالب این است که تضادی در بهبود میزان تولید و بهبود راندمان مصرف انرژی وجود ندارد. برخلاف اتومبیل که در آن با افزایش سرعت میزان راندمان مصرف پایین می آید، در اکسترودرها با افزایش نرخ تولید، راندمان مصرف انرژی نیز بهبود می یابد؛ بنابراین افزایش سرعت تولید (Kg/h) همانطور که در شکل 4 نشان داده شده، سبب کاهش هزینه ها می شود.اگرچه، میزان کاهش هزینه و افزایش راندمان انرژی با افزایش میزان سرعت تولید، رابطه خطی نیست
(y=AX-1+B ) و بهبودها نیز خطی نیستند. هنگامی که نرخ تولید بالا است، افزایش بیشتر آن ممکن است فقط سبب بهبود اندکی در راندمان مصرف انرژی و یا کاهش هزینه گردد. با این روش بهبود واقعی تنها وقتی به دست می آید که نرخ تولید پایین است.
کارکرد بالای موتور
عملکرد بالای موتور سبب افزایش راندمان نسبی مصرف انرژی در فرایند می شود اما در این حالت نیز بیشترین مصرف انرژی در موتور اصلی است. درصد مصرف انرژی موتور بسته به شرایط فرایند تغییر می کند، اما متغیرهای اصلی در واحدهای تولیدی بعد از اکسترودر هستند؛ مثلاً در تولید پروفیل، کالیبراتورها هستند.
با توجه به اینکه موتور اکسترودر در حدود 66% انرژی ورودی به آن را مصرف می کند، انتخاب صحیح موتور اولین قدم در بهبود مصرف انرژی است. موارد بسیاری در موتورها وجود دارندکه باید در نظر قرار گیرد. اما صرفه نظر از نوع موتور، اساسی ترین کار، انتخاب سایز مناسب موتور اکسترودر برای هر تولید است. همواره باید طراحی اکسترودر و مارپیچ کنترل شود تا اطمینان یابید که آنها مناسبترین انتخاب برای نوع محصول و تولید مورد نظرتان هستند.
اکسترودرها وقتی که در شرایط طراحی کار کنند، بیشترین راندمان را دارند( در همه موارد از جمله مصرف انرژی) تا جایی که امکان دارد، اکسترودر باید در حداکثر سرعت طراحی کار کند که معمولاً سرعت بهینه برای گرمایش و تولید بهینه است. سرعت مارپیچ باید به گونه ای تنظیم شود که نرخ تولید اکسترودر به میزان ماکزیمم نزدیک است و در عین حال کیفیت نیز مناسب باشد.
انتخاب صحیح موتور اکستروژن
در بیشتر اکسترودرهای قدیمی از موتورهای DC استفاده می شد و کنترل سرعت مارپیچ اکسترودر توسط آن انجام می گرفت، اما امروزه در اکسترودرهای مدرن از موتورهای AC با سرعت های متغیر استفاده شده تا سرعت بهتر قابل کنترل باشد. در جدول زیر خلاصه ای از این دو روش ارائه شده است.
در دسترس بودن رنج وسیعی از موتورهای AC با کنترل VSD(Variable Speed Drivers) آنها را به عنوان بهترین انتخاب در ماشین های جدید فراهم می کند و بسیاری از تولید کنندگان اکسترودر اکنون موتور DC را از محصولات خود خارج کرده اند. VSD ها می توانند جهت تطابق موتورها برای کارکرد در پایین ترین سرعت ممکن ( در رنج ترک مجاز) به کار روند و میتوانند طوری تنظیم شوند که میزان مصرف انرژی را کاهش دهند.
در گزارشات جمع آوری شده در این تحقیق، میزان صرفه جویی متوسط انرژی با این روش در حدود 10-7% بوده است، اما در تحقیقات دیگر صرفه جویی تا بالای 20% نیز بسیار گزارش شده است. میزان دقیق صرفه جویی بستگی به نوع ماشین و میزان سرعت دارد. در برخی موارد حتی شاهد 30% مصرف انرژی نیز بوده ایم.
بنابراین:
1- واحدها همواره باید از موتورهای AC دارای VSD برای اکسترودرهای جدید خود استفاده کنند. مورتور های AC باید دارای رتبه بندی IE3 باشند.
2- یکی از صرفه جویی هایی که در استفاده از موتورهای AC با VSD در نظر گرفته نشده است، کاهش قابل توجه در انرژی نگهداری آنها است.
شکل 4- هزینه های انرژی بر حسب نرخ تولید
بهینه سازی موتورهای AC+ VSD
این امر به راحتی بر روی موتورهای AC+ VSD قابل انجام است که کاملاً توصیه می گردد. میزان صرفه جویی انرژی در این حالت درحدود 20-5 درصد خواهد بود، اما کاهش هزینه نگهداری قابل توجه است. برگشت سرمایه این کار یک تا دو سال است. واحدها باید به فکر تعویض موتورهای DC خود نیز با موتورهای AC+VSD دارای رتبه بندی IE3 باشند.
انتقال نیرو به مارپیچ
گیربکس نیاز به هزینه نگهداری بالایی دارند.
نکته ها:
1- هرگز از مقدار ترک مجاز گیربکس بالاتر نروید.
2- اطمینان بیابید که روغن گیربکس در دمای مناسب است. اگر دما خیلی بالا باشد، احتمالاً گیربکس یا سیستم روان سازی دچار اشکال شده است. اگر دمای آن خیلی پایین باشد، روان سازی غیر موثر است.
3- لرزش بالا معمولاً نمایانگر وجود اشکال است.
اقدامات توصیه شده
بهبود راندمان انرژی یک واحد و یا اکسترودر موجود، به راحتی قابل انجام بوده و با بکارگیری بیشتر تجهیزات یا به حداقل رساندن بار پایه صورت می گیرد.
بسیاری از اقدامات دیگر نیز وجود دارد که به ویژه در بخش سرویس دهی و نگهداری باید انجام گیرند، اما یکی از مهمترین اقدامات دراز مدت از این که اطمینان یابید اکسترودرها دارای بهترین راندمان مصرف انرژی هستند، این است که از تکنولوژی مناسب در موتور اکسترودر استفاده کنید. در نظر بگیرید که متوسط زمان کارکرد اکسترودر 15 سال است و در این بازه طولانی مدت ، هزینه انرژی مصرفی بسیار بیشتر از سرمایه گذاری اولیه اکسترودر خواهد بود.
Comments