بهره وری انرژی؛ فرآیند آینده
مدیریت انرژی در فرآیند اکستروژن لوله و پروفیل
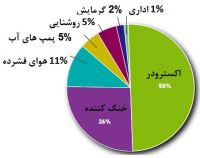
سرویس ترجمه انجمن لوله و اتصالات پی وی سی، رابین کنت (Robin Kent) که سمت مشاور را عهده دار است، میگوید؛ در شرایط سخت کاری، شرکتها معمولاً به کاهش تعداد نیروهای انسانی خود فکر میکنند. اما با رویکردی دقیق میتوان با مدیریت انرژی، به صرفهجویی قابل توجهی در هزینهها دست یافت.
هزینهها در یک کارخانه اکستروژن خیلی هم ارزان نیست، بسیاری از آنها ـ مانند آب خنککننده ـ واقعاً گران هستند، رهایی از این هزینهها میتواند موجب صرفهجویی مالی برای شما شود.
در تعریف اکستروژن میتوان اینگونه گفت که؛ فرآیندی است که به شدت به برق وابسته است و عمده مصرف انرژی در یک واحد اکستروژن در عملیات اکسترودرها است. برای اکستروژن لوله و پروفیل، حدود 50 درصد از تمام انرژی در اکستروردرها مورد استفاده قرار میگیرد، باقیمانده انرژی برای خدمات و لوازم جانبی مصرف می شود.
هزینههای انرژی در اکسترودرها ممکن است کمی بالا باشند، اما بازگشت سریع سرمایهگذاری در این صنعت، توجیه منطقی برای استفاده از این انرژیها است. اکسترودرهای قدیمیتر از موتورهای DC استفاده میکردند اما نسل جدید اکسترودرها اغلب با موتورهای AC که توسط درایو سرعت متغیر (VSD) کنترل میشوند، در دسترس هستند. کنترلکننده VSD در موتورهای AC در بسیاری از اکسترودرها استفاده میشوند و استفاده از آنها به شدت توصیه میشود.
با هر نوع موتوری، دستگاه اکسترودر باید متناسب با محصول موردنظر، انتخاب شود. طراحی اکسترودرها به گونهای است که بالاترین میزان کارایی را (نه تنها در بحث انرژی) دارا باشند. در حد امکان، اکستروردها باید با بالاترین سرعت طراحی شوند، که آن سرعت معمولا همان کارآمدترین سرعت است. سرعت مارپیچ باید به گونهای کنترل شود تا سرعت اکستروژن نزدیک سرعت ماکزیمم باشد و همچنان محصول خوبی تولید کند.
موتورهای اکسترودر معمولاً با سرعت بالا کار میکنند و در سرعت موردنیاز مارپیچ تنظیم میشوند. زمانی که نسبت دندههای موجود برای این کار مناسب نباشد، موتورها با سرعت صحیح کار نمیکنند، مصرف انرژی بیش از اندازه خواهد بود و گشتاور ایجاد شده بسیار پایینتر از سطح مطلوب خواهد بود. تغییر نسبت موتور و درایو میتواند یک پروژه ساده برای بهینهسازی کاربرد موتور باشد.
شکل 1. مشخصات مصرف انرژی در یک واحد معمولی اکستروژن
با تمرکز بر روی بیشترین مصرفکننده انرژی برای رسیدن به سریعترین نتیجه
گرما دهی و خنک کاری
بیشترین میزان انرژی گرمایی موردنیاز برای پلاستیسایز کردن (نرمکردن) و گرمکردن پلاستیک توسط گرمای حاصل از اصطکاک مواد که در مارپیچ حرکت میکنند، ایجاد میشود. در بیشتر موارد، انرژی مکانیکی در انتقال گرما به داخل مواد از انرژی خارجی هیتر که تنها روی لایه خارجی مواد در سطح سیلندر عمل میکند، موثرتر است. این انرژی میتواند گرمای اصطکاکی را که به وسیله تولید یک لایه مذاب در سطح داخلی سیلندر به وجود آمده را کاهش دهد.
با بهینهسازی سرعت اکسترودر گرما توسط کار مکانیکی به حداکثر میزان خود میرسد و این مساله سبب کاهش مقدار انرژی الکتریکی موردنیاز برای گرمکردن پلاستیک میگردد. زمانی که تجهیزات پاییندستی خروجی را محدود نکنند، مصرف انرژی در یک اکسترودر (in kwh/kg) میتواند حدود 50 درصد به وسیله دو برابر کردن سرعت چرخش مارپیچ کاهش یابد. در صورتی که گرمای حاصل از اصطکاک بیش از حد باشد، از فنهایی برای حذف گرمای اضافی از سیلندر استفاده میشود. خنککردن سیلندر به عملکرد بهتر اکسترودر کمک میکند، همچنین موجب افزایش اصطکاک در سطح پلاستیک/سیلندر و اختلاط بهتر و حرکت مواد رو به جلو میگردد.
کنترل دمای سیلندر
1. کنترلکنندههای اکسترودر را چک کنید تا مطمئن شوید که سیستم گرمادهی و خنککاری با یکدیگر خوب کار میکنند و در رقابت با یکدیگر نیستند. اطمینان حاصل کنید که بین هیترها و دمندهها یک «بخش مرده» وجود داشته باشد.
2. کنترل دقیق دما سبب تولید یک محصول خوب و به حداقل رسیدن مصرف انرژی میگردد.
3.عایقبندی سیلندر یک روش موثر است اما مناسب برای همه بخشهای سیلندر و یا همه کاربردهای سیلندر نیست. نصب عایق در همه بخشهای سیلندر میتواند منجر به «فرایند فرار» شود.
با بررسی هیترها و فنهای سیلندر میتوان به فهم دقیق جریان گرما در یک اکسترودر/محصول ویژه و همچنین زمان روشن و خاموش شدن هیترها و فنها پی برد (هیتر و فن در یک زمان خاموش و روشن نمیشوند). در یک فرآیند اکستروژن خوب باید پلاستیک در دمای مطلوب نگه داشته شود، اما از (گرمای بیش از حد) آن جلوگیری گردد. این مسئله بستگی به مواد دارد، در فرآیند تولید پنجره که یک فرآیند کوچک است . گرمای بیش از حد ناشی از برش شایع است، مگر اینکه کنترل دما دقیق باشد. اگر هیترها به طور پیوسته روشن باشند، پس موتور قادر به تامین میزان کافی حرارت برشی برای فرآیند نمیباشد، در این صورت دو انتخاب وجود دارد:
1. اکسترودر اصلی میتواند گرمای برشی بیشتری تولید کند در این صورت نیاز به هیترها کاهش مییابد. این کار، یک گزینه پیشنهادی مناسب است اما ممکن است تولید گرما توسط تجهیزات پاییندستی خنککننده محدود شود.
2. سیلندر میتواند توسط عایق برای کاهش گرمای از دست رفته عایق شود اما این کار به ندرت بر روی یک سیلندر کامل صورت میگیرد. بخش عقبی به دلیل ورود مواد سرد که قبل از آن تحت هیچ نوع برشی نبودهاند، نیاز به گرمای پیوسته دارد و بخش جلویی سیلندر به علت کاهش گرمای برشی ممکن است در این ناحیه نیاز به گرما داشته باشد. هنگامی که گرمای برشی کم است، عایقبندی سیلندر در کاهش انرژی ورودی موردنیاز از هیترها مفید و موثر است. این کار سبب صرفهجویی در مصرف انرژی، کاهش نوسانات دمایی و افزایش رعایت مسائل بهداشتی و ایمنی میشود.
کنترل تجهیزات پاییندستی
گرمای برشی خیلی کمی در تجهیزات پاییندستی مثل نوک مارپیچ وجود دارد از این رو هیترها همیشه برای نگهداشتن پلاستیک در دمای درست در بین صفحات، آداپتورها، لولههای انتقالدهنده و دایها موردنیاز هستند. این کار برای محصولات توخالی که مندرل در محل توسط اسپایدرها نگه داشته شده و جوش کامل جریان مذاب باید بعد از عبور مواد از اسپایدر اتفاق بیفتد(در غیر این صورت ضعف محسوب میشود).
انواع تجهیزات پاییندستی
1. همه قسمتهای تجهیزات پاییندستی نوکپیچ برای کاهش تغییرات دمایی و مصرف انرژی باید عایقبندی شوند.
2. ماکزیمم سرعت قابل قبول برای اکسترودشدن بعد از خنککاری را بیابید و دمای آب خنک کننده را برای رسیدن به این هدف تنظیم کنید. محصول را نباید بیش از حد سرد کنید.
3. بررسی کنید که دمای آب خنککاری مناسب باشد و همچنین هدر نرود، سرد باشد و به طور موثر توزیع شده باشد. از گردش آب در میان دستگاههای خاموش و کالیبراتورها جلوگیری کنید، جریان آب سرد را در ماشینهای خاموش، متوقف کنید.
4. بررسی کنید، حداقل میزان موردنیاز ذخیره پمپ خلاء برای تولید و توزیع مناسب باشد. زمانی که موردنیاز نیست پمپ خاموش باشد.
5. از VSDها (با حلقههای بازخورد) روی پمپهای خلاء برای کنترل حداکثر میزان خلاء بدست آمده، استفاده شود.
6. بررسی کنید که مخازن خنککننده مورد استفاده در خلاء برای کاهش استفاده از خلاء به طور صحیح بسته شده باشند.
گرما معمولاً برای همه نواحی پاییندستی نوک مارپیچ لازم است و اتلاف گرما نیز قابل توجه است. عایقبندی سبب کاهش اتلاف گرما و همچنین میزان مصرف انرژی در این نواحی میشود، به خوبی نیز باعث افزایش سلامتی و ایمنی میگردد.
کالیبراسیون و خنککاری در یک زمان مشابه انجام میشود گرچه انواع روشهای مختلفی مورد استفاده قرار میگیرد. برای پروفیلهای ساده، کالیبراسیون یک تکصفحه در یک حمام آبِ سرد صورت میگیرد، در حالیکه برای پروفیلهای پنجره چندلایه PVC-U کالیبراسیون معمولاً توسط کالیبراتورهای صفحه فلزی در یک حمام آب سرد یا توسط اسپری آب صورت میگیرد.
کارایی خنککننده فاکتور کنترلی برای سرعت کلی خط میباشد. پروفیل باید در زمانی که در آب خنککننده قرار میگیرد، کاملاً خنک شود و اگر خنککاری موثر نبود در این زمان سرعت خط باید کاهش یابد. بسیاری از واحدهای لوله و پروفیل به آب خنککننده به عنوان یک منبع رایگان نگاه میکنند و اجازه میدهند آب سرد حتی در زمانهایی که مورد استفاده قرار نمیگیرد، آزادانه جریان داشته باشد.
این آب گرم شده مجدداً وارد چیلر میشود و دوباره با هزینههای بالا سرد میشود. پمپهای خلاء برای حذف هوا از سیستم آب و همچنین برای ایجاد سطح تماس خوب بین اکسترودشده و سیستم کالیبراسیون مورد استفاده قرار میگیرند. آنها معمولاً دارای سرعت ثابت و کنترلنشده هستند.
در نتیجه، اکسترودرهای لوله و پروفیل فرصتهای بسیاری برای کاهش مصرف انرژی و قیمت بدون سرمایهگذاری قابل توجه دارند. آنها میتوانند راهکارهای سادهِ بسیاری را که هیچ اثر زیانآوری روی محصول یا عملکرد دستگاه ندارد، برای کاهش قیمت انجام دهند.
انواع اکسترودر
1. همیشه در مرحله تصمیمگیری برای خرید، کارایی انرژی را در نظر بگیرید.
2. همیشه گزینه موتور VSD+AC را برای خریدهای جدید در نظر بگیرید و موتورهای موجود را با موتورهای VSD+AC مجهز کنید.
3. استفاده از اکسترودرهای بزرگ برای تولید محصولات کوچک موجب اتلاف انرژی و همچنین هزینههای مالی میشود.
4. گزینه تغییر موتور اکسترودر را برای مطابقت با کار مدنظر، بررسی کنید.
5. هزینههای زمان و مصرف انرژی با تغییر موتور ذخیره میشوند. محاسبات نشان میدهند که تغییر موتور یک عملیات بسیار موثر در کاهش میزان هزینهها است.
6. بررسیها نشان میدهند که اصلاح بارگیری و اندازه موتورهای اکسترودر و همچنین بهینهسازی نسبت دندهها موجب صرفهجویی انرژی میگردد.
7. در جایی که درایو از قرقرهها استفاده میکند، به سادگی میتوان از قرقرهها با سایزهای مختلف استفاده کرد اما باید مطمئن شد که هنگام تغییر قطرها، هماهنگی بین قرقرهها وجود دارد.
شکل 2. توابع مختلف دارای نیازهای مختلف انرژی میباشند. این طرح بخش عمده مصرف انرژی را در گرمایش نشان میدهد. درایو اکسترودر گرمایش برشی موردنیاز را ارائه نمیدهد و عایقبندی سیلندر مورد توجه قرار گرفته است.
* تهیه و ترجمه: سمیه صلاحی (شرکت پارس پولیکا)
Comments