pvc-asso.ir
عوامل موثر در کیفیت رزین PVC
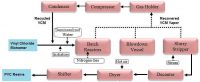
انجمن لوله و اتصالات پی وی سی:
1- مونومر وینیل کلراید
ونومر VCM مورد استفاده در تهیه PVC باید خالص باشد
ناخالصی ها سبب انجام واکنش های ناخواسته می شود. مقادیر هیدروکربن های کلرینه شده اگر بیشتر از حد مجاز ( نرمال) باشد به عنوان عامل انتقال زنجیره عمل می کند که سبب آلودگی، کاهش کیفیت PVC تولید شده و یا در بخش بازیابی مونومر تجمع کرده و مشکل فرایندی ایجاد می کند. ناخالصی آب در خوراک سبب افزایش سرعت خوردگی در تجهیزات واحد می شود که بسیار ناخواسته است. آهن حاصل از خوردگی نیز مونومر CM را آلوده می کند که سبب تاثیر سویی بر عملیات پلیمریزاسیون و تولید اکسید وینیل می شود. اکسید وینیل حاصل بسیار ناپایدار بوده و به مواد دیگر تجزیه می گردد. در این حالت پایداری حرارتی PVC تولید شده پایین می آید و تغییر رنگ سوسپانسیون در برج های گاز زدایی و درایرها زود مشاهده می شود. برای حل این مشکل نسبت مونومر بازیابی شده به خالص مصرفی کنترل می شود تا کیفیت محصول PVCپایین نیاید. با استفاده از ماده آنتی اکسیدانت دی ترشیو بوتیل پاراکرزول می توان اثر اکسیژن را حذف کرد. سایر ناخالصی ها مانند هیدروکربن های غیر اشباع و ممانعت کننده های واکنش تاثیر نامطلوب بر روی مورفولوژی ذره PVC دارند.
سایر افزودنی ها
وقتی VCM پلیمریزه می شود مقدار HCL تشکیل می شود که ممکن است PH محلول آبی سوسپانسیون را پایین بیاورد. CO2 نیز از تجزیه آغازگرها آزاد می شود و همین اثر را دارد. تغییرات PH بر روی تعلیق کننده ها و نحوه ی عمل آنها تاثیر نامطلوب دارد برای حل این مشکل استفاده از مواد بافر و قلیایی ضروری است(Nahco3 و Ca(OH)2)
استفاده از آنتی فولینگ در راکتورهای بزرگ بخصوص انواعی که به رفلاکس کندانسور مجهزند قویا توصیه می شود. انواع مختلفی از آنتی فولینگ ها استفاده می شود اما ترکیباتی که پایه فنلی دارند معمولا موثرترند و بیشتر استفاده می شود( پلی آریل فنل)
2- میزان دز مواد تعلیق کننده و اثرات آن
1- تزریق کم مواد تعلیق کننده به راکتور سبب افزایش زیاد اندازه ذرات PVC در راکتور می شود. این پدیده را coarse شدن می نامند و سبب تولید ضایعات فراوان، اخلال در عملیات جداسازی، گرفتگی سینی های برج گاز زدایی و درایر می شود
2- تزریق زیاد از حد مواد تعلیق کننده به راکتور سبب ریز شدن اندازه ذرات pvc می شود. علاوه بر کیفیت، سبب بروز فوم در راکتور، اخلال در عملیات جداسازی برج های گاز زدایی و غربال های درایر می شود.
3- تزریق بیش از حد تعلیق کننده S2 اثر شدیدی بر دانسیته بالک پودر PVC دارد و سبب افزایش بیش از حد تخلخل می گردد و سبب کاهش ظرفیت درایر ( بخش غربال) و همچنین اکسترودر در صنایع پایین دست می شود.
4- تزریق کم تعلیق کننده S2 سبب افزایش دانسیته بالک و کاهش تخلخل PVC تولیدی می شود و به نوبه خود جذب نرم کننده ها را در صنایع پایین دست کاهش می دهد.
3- راندمان راکتورهای PVC
راکتورها تجهیزات اصلی در تولید PVC هستند. در راکتورها پلیمریزاسیون PVC که یک واکنش گرمازاست صورت می گیرد. بنابراین راندمان یک راکتور در توان آن در انتقال حرارت در واحد زمان ناشی می شود. در واکنش گرمازای راکتور و میزان حرارتی که می تواند آزاد کند از رابطه ی زیر پیروی می کند:
Q= مقدار حرارتی که توسط سیال خنک کننده راکتور منتقل می شود
U= ضریب انتقال حرارت
A= سطح انتقال حرارت
= تفاوت بین دمای راکتور و دمای سیال خنک کننده
4- توزیع اندازه ذرات (PVC (PSD
یکی از مهم ترین موضوعات در تولید PVC، کنترل توزیع اندازه ذرات محصول نهایی در فرایند تولید است. توزیع اندازه قطرات مونومر اولیه و همچنین PSD در محصول نهایی به نوع و غلظت محافظ های کلوئیدی ( تعلیق کننده ها)، سرعت همزن در راکتور و خواص فیزیکی فازها( دانسیته، ویسکوزیته و کشش سطحی) در راکتور بستگی دارد. هر چه قدر ذرات PVCتولیدی کروی باشند( به حالت کروی نزدیک تر باشند) دانسیته بالک افزایش می یابد. بنابراین تشکیل فوم در عملیات پلیمریزاسیون و جداسازی مونومر باقیمانده کمتر است.
5-عملیات هم زدن( اختلاط)
اندازه قطرات VCM که نهایتا منجر به اندازه ذره PVC می شوند تحت تاثیر سرعت همزن راکتور شکل می گیرند. همزن انرژی مکانیکی را برای غلبه بر چسپندگی مولکول های مونومر ایجاد نموده و قطراتی با قطر حدود 40 میکرومتر ایجاد می کند. بدون وجود همزن، مخلوط پلیمریزاسیون به دو فاز مایع در بالا و فاز پلیمر جامد در پایین راکتور تفکیک می شود. اندازه ذرات و توزیع آن به توان همزن ، حجم و غلظت سوسپانسون ربط دارد. پارامتر های موثر اختلاط با استفاده از عدد بدون بعد وبر مشخص می شود.
6- آب پروسس(DM)
آب پروسس( آب بدون مواد معدنی) نقش مهمی در تولید SPVC دارد.
آب تعلیق کننده ها را حمل می کند و بیشتر آنها در آب حل می شوند
بنابراین خلوص آب، ویژگی مهمی از فرایند سوسپانسیونی می باشد و آب با کیفیت برای کنترل دقیق و پایداری مورفولوژی ذرات ضروری است و بایستی از آب DM استفاده شود. آبی که سختی داشته باشد محصولی با دانسیته بالک بالا ایجاد می کند. اندازه ذرات بیش از حد درشت می شود و این پدیده را coarse شدن می نامند.
واکنش تولید pvc گرمازاست و آب به دلیل داشتن ظرفیت گرمایی بالا نقش مهمی نیز در انتقال حرارت و ایمنی واکنش دارد. آب تاثیر مهمی بر کنترل ویسکوزیته سوسپانسیون در راکتور دارد به نحوی که از افزایش بار همزن (kw ) جلوگیری می کند. در صورت افزایش بار همزن، آب به راکتور اضافه می شود.
7- نسبت VCM/H2O
این نسبت به میزان زیادی به توان موتور همزن راکتور و قابلیت انتقال حرارت در راکتور بستگی دارد. اگر ویسکوزیته سوسپانس بالا باشد مشکل کنترل حرارت بروز می کند و الکتروموتور همزن ممکن overload شود. این مشکل را میتوان با تزریق مقدار اضافی از آب DM به راکتور در مرحله پلیمریزاسیون حل نمود. اگر چنانچه میزان آب کمتر از حد مطلوب باشد، محصول PVC با اندازه ذرات بسیار درشت تولید می شود. همچنین دانسیته بالم محصول PVC در این حالت افزایش می یابد.
منبع: سمینار تیم پژوهشی PVC پتروشیمی اروند
نظرات