pvc-asso.ir
راهنمای عیب یابی اکستروژن
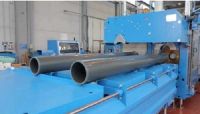
سرویس ترجمه انجمن لوله و اتصالات پی وی سی:
شرح مشکل |
علت های ممکن و راه های پیشنهادی |
زمان میکس در میکسر گرم طولانی است |
سطوح پرکنندگی پایین است.بار حجمی میکسر را تا رسیدن به حد مطلوب افزایش دهید. |
پوشش های ضخیم بر دیواره داخلی میکسر گرم |
ترتیب اشتباه افزودن مواد اولیه، ترتیب خوراک میکسر را تغییر دهید |
تخریب حرارتی مخلوط خشک |
حداکثر دما در میکسر گرم خیلی بالاست، دما را کاهش دهید. |
کلوخه شدن در مخلوط خشک |
|
مخلوط خشک به صورت آزاد جریان ندارد |
|
تراکم(جمع شدگی) در میکسر خنک کننده |
خنک شدن سریع مخلوط خشک راهکار: افزایش دمای آب خنک کننده یا کاهش سرعت جریان آب خنک کننده
|
پوشش در دیواره های داخلی میکسر خنک کننده |
|
زمان میکس در میکسر خنک کننده خیلی طولانی است |
|
سطح پوست کوسه ای |
شکستگی مذاب، دمای پایین تر در سر و قالب اکسترودر ، تمیز کردن تجهیزات |
حباب یا تخلخل در نمونه اکسترود شده |
|
رگه های قهوه ای |
پلیت اوت (رسوب افزودنی ها) و سوختن، سر و قالب اکسترودر را تمیز کنید |
خوراک دهی اکسترودر به درستی انجام نمی شود |
بخش خوراک خیلی گرم است.قیف خوراک و فیدر را سرد کنید. دمای بخش خوراک اکسترودر را کاهش دهید. |
علائم فرورفتگی |
از دست دادن فشار در قالب، نمونه اکسترود شده کالیبر را دیر پر می کند. فشار را در دای افزایش دهید یا فرمولاسیون مخلوط خشک را تغییر دهید برای مثال با افزودن اصلاح کننده جریان |
تغییر رنگ |
|
رگه های رنگی تا سیاه |
توزیع نامناسب رنگدانه ها، بهبود فرایند میکس و استفاده از رنگدانه هایی با قابلیت پخش بالا |
نوسان جریان |
پلیت اوت در قالب گرم کننده قالب کار نمی کند، گرم کننده قالب را بررسی کنید کافی نبودن گاز گیری، ناحیه گازگیری را تمیز کنید، دماهای سیلندر را بهینه کنید، کامپاند و فرایند اختلاط همچنین فرمول مخلوط خشک را بهبود دهید. |
سرعت خیلی پایین خروجی |
مخلوط خشک دارای بار استاتیک است فرسایش مارپیچ یا سیلندر نوسان در دانسیته بالک یا سرعت تغذیه مخلوط خشک سطح پرکردن مارپیچ خیلی پایین است مکش مارپیچ مطلوب نیست دمای ناحیه مکش مارپیچ خیلی بالاست پل زدن در قیف خوراک |
سطوح موجدار داخلی |
دمای توده ی جرمی خیلی زود فرا رسیده است. سطوح ژلینگی را در ناحیه گازگیری بررسی کنید. ژلینگی را با افزودن روان کننده خارجی به تاخیر بیاندازید( مانند وکس های پارافین) یا دمای سیلندر را کاهش دهید. دمای مارپیچ خیلی بالاست جریان بهینه نیست. صفحه شکن موثر برای دستیابی به جریان برگشتی افزایش یافته نصب شود. قابلیت میکس در ناحیه سنجش مارپیچ خیلی پایین است. |
براقیت پایین |
اگر براقیت با زمان کاهش یابد، تشکیل پلیت اوت می تواند یکی از دلایل باشد درجه پلاستیکی شدن پایین است که می تواند با راهکارهای زیر بهبود یابد:
استفاده از مواد معدنی بیش از حد درشت( به عنوان مثال گچ)، استفاده از مواد با کیفیت ریزتر و گریدهایی با پراکندگی بهبود یافته رطوبت بالا در مخلوط خشک رطوبت بالا در انتقال هوا
|
خزش مواد به سمت ناحیه گازگیری |
مارپیچ خیلی پر باشد( به علت دانسیته بالای مخلوط خشک) ژلینگی بهینه نیست و مواد هنوز به صورت پودر است، دما را در زون ها افزایش دهید. فشار توده ی جرمی خیلی بالاست. مارپیچ و سیلندر نشانه هایی از فرسودگی و سایش دارد. دماهای پایین تر خروجی زون و مارپیچ ها افزایش دما بعد از ناحیه گازگیری |
سطوح خارجی موجدار |
پلاستیکی شدن به دلیل وکس پلی اتیلن اکسید شده بیش از حد پیشرفت کرده است. وکس پلی اتیلن اکسید شده را کاهش دهید. پلاستیکی شدن به علت اصلاح کننده جریان زیاد، پیشرفت کرده است. اصلاح کننده جریان را کاهش دهید. پلاستیکی شدن به علت دمای بالا خیلی پیشرفت کرده است، دما را کاهش دهید. پلاستیکی شدن به علت جریان بالای مواد خیلی پیشرفت کرده است. جریان مواد را کاهش دهید. به علت فقدان فشار، مواد بسیار کم اکسترود می شود.خروجی را افزایش دهید دماهای متغیر برای 4 نقطه گرمایشی. زون های حرارتی را باهم هماهنگ کنید. |
پودر در ناحیه گازگیری |
پلاستیکی شدن خیلی به تاخیر می افتد، کلسیم استئارات را افزایش دهید.بارگیری مارپیچ یا دما را در زون ها افزایش دهید. |
خصوصیات مکانیکی پایین |
|
شرینکیج خیلی بالاست |
ژلینگی کافی نیست خواص جریان تغییر کرده است فرسودگی و سایش قالب فرسایش کالیبراتور اختلاف دمای بالا و پایین توده |
نوسان در کل فرایند |
انبارش 24 ساعت بعد از میکس برای برخی ترکیبات خشک مشاهده نمی شود مقیاس ها، میکسر و پارامترهای میکس را بررسی کنید تنوع در کیفیت مواد خام نوسان در سطوح پر شدن نوسان در دانسیته بالک مخلوط خشک |
تغییر در ضخامت دیواره |
نوسان ذوب، دمای مذاب را در سر و قالب اکسترودر کاهش دهید، طراحی مارپیچ را بهبود دهید. |
لکه ها یا نقطه های سیاه روی سطح محصول اکسترود شده |
|
اثر چسپش- لغزش |
|
لکه در محصول اکسترود شده/ پروفیل |
|
سایش واحد کالیبراتور |
|
سایش قالب |
|
نظرات