مدلسازی و شبیه سازی خط تولید عملیات خشک کردن پودر PVC:
مطالعات تجربی و تئوری سینتیک خشک کردن در مقیاس ذرات* (بخش دوم و پایانی)
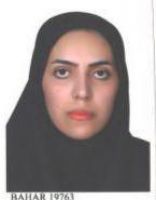
شکل b و a9 یک نمونه از نتایج بدستآمده با شرایط آزمایشگاهی که در جدول 2 لیست شده را نشان میدهد (آزمایش 1). میتوان مشاهده کرد که:
- زمان خشککردن حدود 30ثانیه، بسیار نزدیک به زمان پاسخ رطوبتسنجها است،
- یک تاخیر 3ثانیهای با توجه به تزریق نمونه و زمان موردنیاز برای رسیدن هوای مرطوب رطوبتسنج وجود دارد،
- رطوبت مطلق هوا و نرخ جریان هوای خشک یک سیر تکاملی مشابه دارند،
- کاهش دمای بستر در طول آزمایش زیر
1 باقی میماند که این امر نشاندهنده تاثیرات همدمایی شرایط آزمایش است.
در شکل 8 روند نرمال منحنی زمان رطوبت جامد برای آزمایشات مختلف در شرایط یکسان، نشان داده شده است (نمونههای 1، 2و3). این شکل نشان میدهد سیستم آزمایشی ما تکرارپذیر بوده و واریانس t50 کمتر از 1 ثانیه است.
6. نتایج تجربی
در جدول 2، مجموع دادههای تجربی (دمای بستر سیال، رطوبت مطلق هوای ورودی و سرعت هوا) و مشخصه زمانها: t25، t50 و t75، ارائه شده است. علاوه بر این، رطوبت اشباع هوا (معادله5) نیز در این جدول ارائه شده است.
تاثیر دمای بستر سیال، سرعت هوا و رطوبت اولیه هوا بر سینتیک خشک¬کردن در شکل¬های 11و12 ارائه شده است. این شکل¬ها نمایانگر این مطلب هستند که سینتیک خشک¬کردن حتی در دماهای پایین نیز سریع است. در شرایط عملیاتی، زمان خشک¬کردن زیر 85 ثانیه باقی می¬ماند. دانستن این نکته حایز اهمیت است که این بالاتر گرفتن زمان خشک¬کردن به دلیل زمان پاسخ¬دهی رطوبت¬سنج است. این نتایج همچنین نشان می¬دهد که حتی در یک خشک¬کن همزن دار، در بستر سیال، مقاومت در برابر انتقال خارجی قابل اغماض نیست. این مقاومت، به وسیله پارامترهای هیدرودینامیکی سیستم کنترل شده و شامل تبادل انرژی و جرم بین اتمسفر خشک¬کن و ذرات پی¬وی¬سی می¬باشد.
به علاوه چنانچه در نتایج تجربی ارائه شده در شکل 10 مشاهده می¬شود، افزایش میزان هوا از 9/2 تا kg/h 12/4زمان خشک¬کردن را از 53 تا 36 ثانیه کاهش می¬دهد. این امر موجب افزایش سرعت نسبی بین هوا و ذرات میگردد. از این رو، انتقال جرم و حرارت افزایش یافته در نتیجه زمان خشککردن کاهش مییابد. با توجه به آنچه که در شکل 11 مشاهده میشود، افزایش دمای بستر سیال از 35 به 55 زمان خشککردن را از 40 تا 24 ثانیه کاهش میدهد. در واقع، افزایش دمای بستر سیال سبب بهبود انتقال حرارت بین بستر سیال و ذرات شده، همچنین نیروی موردنیاز برای انتقال جرم را فراهم میکند
).
در شکل 12 اثر رطوبت هوا بر سنتیک خشککردن و مشخصات زمان خشککردن و منحنی نرمال رطوبت جامد بر زمان مشاهده میشود. این نتایج نشان میدهند که، افزایش رطوبت مطلق هوا از 16 تا هوای خشکkg/g آب 25 زمان خشک کردن را از 55 به 84 ثانیه افزایش میدهد. این امر را می توان به عنوان تاثیر نیروی محرکه خشک کن توجیه کرد؛ افزایش رطوبت اولیه منجر به افزایش Y و بنابراین کاهش عملیات خشک کردن میشود. همه این نتایج نشان میدهند که سینتیک خشک کردن ذرات PVC متاثر از هر دو انتقال خارجی و داخلی رطوبت است.
7. مدل سینتیک
برپایه نتایج تجربی بدست آمده و اطلاعات موجود در رابطه با خواص پودر PVC، قانون سینتیک را تعیین کردیم. این قانون در گردآوری نتایج تجربی ما اجرا و منجر به ایجاد شبیهسازی مدل سینتیک گردید. در این مرحله، فرضیه و معادلات این مدل را شرح دادیم، و، با توجه به آن اعتبار نتایج تجربی بدست آمده را سنجیدیم.
7-1. فرضیه و معادلات
این نکته مشخص است که سطح ذرات PVC تمایل کمی به آب دارند، در نتیجه خشککردن داخل ذرات میتواند با راندن بخار از سطح به داخل هسته صورت گیرد (شکل13). کاهش سایز هسته را میتوان مبنای این فرضیات قرار داد:
- ذرات کاملا کروی و یکنواخت هستند.
- تبخیر روی سطح اتفاق میافتد.
- سیال در یک مخزن همزندار قرار میگیرد.
- رطوبت هسته تر و پوسته خشک به ترتیب برابر با رطوبت اولیه ذرات (X0) در نظر گرفته میشود و برابر صفر است.
- انتقال جرم توسط نفوذ بخار آب در پوسته خشک و انتقال همرفتی در سطح ذرات صورت میگیرد.
- گرما از طریق هوا و توسط انتقال همرفتی ذرات منتقل میشود و نفوذ در پوسته خشک به وسیله هدایت صورت میگیرد.
- وزن نمونه به اندازه کافی کم انتخاب شد تا از ایزوترمال بودن دمای بستر سیال اطمینان حاصل گردد.
- دمای ذرات یکنواخت در نظر گرفته شد. این فرضیه را میتوان با مقدار کم عدد حرارتی بیو توجیه کرد. در ادامه، این فرضیه با مدل آنالوگ محاسبه پروفایل دمایی، در پوسته خشک، قابل توجیه است.
- پروفایل لحظهای رطوبت هوا در پوسته خشک با فرضیه حالت شبه ساکن بدست میآید.
معادلات مدل با حل تغییر متغیر و استفاده از روش رانگ ـ کوتا، که در زیر ارائه شده، به دست آمد.
- دانسیته بخار آب در سطح ذرات
2-7. تاییداعتبار مدل
در شکلهای 14 و 15 نتایج عددی بدست آمده، نمایش داده شده است. این نتایج نشان میدهند که، زمان حقیقی خشککردن حدود 11 ثانیه است، یعنی 4 مرحله سریعتر از زمان مشاهده شده در رطوبتسنج و فرایند سه مرحلهای خشککردن:
- مرحله گرمکردن نمونه، از 0 تا 3 ثانیه (مرحله اول).
- مرحله سرعت ثابت خشککردن، از 3 تا 5/10ثانیه (مرحله دوم)
- کاهش سرعت خشککردن، از 5/10 تا 13 ثانیه (مرحله سوم).
در این مدل، برای مقایسه نتایج عددی با دادههای تجربی، تابع انتقال رطوبتسنج را نیز مورد استفاده قرار گرفت. نتایج تئوری با یافتههای تجربی مورد مقایسه قرار گرفتند (مثال1، 2 و 3)، شکل 15 نمایانگر تطابق خوبی بین پیشبینیهای مدل و دادههای تجربی است.
برای درک بهتری از تاثیر نسبی مقاومتهای داخلی و خارجی بر روی انتقال جرم، حساسیت عدد بیو جرمی مطالعه شد. فرمول آن در زیر یادآوری شده است:
در شرایط شبیهسازی شده قبلی، عدد بیو که با استفاده از مدل، بدست آمد، برابر با 1/44 بوده و نشاندهنده رقابت بین مقاومت به انتقالها بود. در شکل 16، افزایش رطوبت مطلق هوای خروجی بر حسب زمان (در این مدل عدد بیو از 0/1 تا 10 زمان مختلف محاسبه شده است) برای عددهای بیو متفاوت مشاهده میشود. این نتایج نشان میدهند که فرآیند خشککردن برای عدد بیو بزرگ بسیار طولانی و مشکل خواهد بود. بنابراین در این مورد، مقاومت خارجی در برابر مقاومت داخلی ناچیز نخواهد بود. این پدیدهها را میتوان با استفاده از پارامترهای مورفولوژیکی ذرات PVC تشریح کرد. مقاومت داخلی کم به تبخیر آب در ذرات کوچک را میتوان به درشتی خلل وفرج و تمایل کم آنها به آب نسبت داد.
شکل 18 مقایسه بین مشخصه زمانهای ارائه شده توسط مدل و دادههای تجربی را نشان میدهد. این نتایج نشان میدهد که پیشبینیهای مدل مانند: دمای سیال (شکل 17)، رطوبت هوای داخلی بین 0 تا 16 گرم آب/kg هوای خشک (شکل 17)، مایعسازی جریان هوا تا kg/s11 (شکل 17) بر روی مشخصه زمانها، صحیح هستند. علاوه بر این، در نرخ کمتر مایعسازی هوا و رطوبت بیشتر هوای ورودی ( 16 گرم آب/کیلوگرم هوای خشک) مشخصه زمان در مدل، خصوصا در t25 ناچیز گرفته شده است.
این پدیدهها را میتوان با دلایل مختلف توجیه کرد:
- تاثیر رطوبت هوای ورودی و نرخ مایعسازی جریان هوا بر پراکنش کیک. در واقع، یک افزایش در رطوبت هوای ورودی و یا یک کاهش در نرخ مایعسازی جریان هوا موجب بیاعتباری این پدیدهها میگردد.
- تاثیر رطوبت هوا روی تعادل محلی که در محاسبات دخالت داده نشدهاند.
- همگن بودن ذرات PVC (یک اندازه بودن منافذ). در واقع، یک افزایش در رطوبت هوا میتواند منجر به کاهش سرعت خشککردن گردد.
- علاوه بر این، حضور تخلخل در ذرات PVC میتواند این فاصله مشاهدهشده را تشریح کند، خصوصا در پایان فرآیند خشککردن. در این مورد، انتقالها توسط هر دو نیروی مولکولی و نفوذ کادسن کنترل میشوند.
8. مدل خشککن پنوماتیک
هدف از این مطالعه طراحی یک مدل خشککن پنوماتیک (مدل ماکروسکوپیک) در مقیاس سینتیک ذرات که قبلاً به طور مفصل شرح داده شده است. همانطور که در شکل 1 مشاهده میشود، خشککردن طی دو مرحله انجام میشود:
- حذف آب سطحی که توسط یک مکانیسم همرفتی صورت میگیرد،
- حذف آب داخل حفره که توسط مکانیسم همرفتی و نفوذ انجام میشود. در این مرحله کاهش حجم هسته وجود دارد، که در قسمتهای قبل به طور مفصل تشریح گردید.
1-8. فرضیهها و معادلات
در این مدل، دو فاز برای تشریح جریان پایدار که شامل؛ یک فاز رقیق پراکنده (پودر تر) و یک فاز پیوسته در یک خشککن پنوماتیک میباشد، مورد استفاده قرار میگیرد. این مدل براساس مفروضات زیر است:
- توازن جرم، انرژی و مومنتوم بین هر دو فاز، اتفاق میافتد.
- از نیروی اصطکاک بین فاز پراکنده و دیوار میتوان صرفنظر کرد.
- فاز پیوسته، ترکیبی از مخلوط بخار آب و دیگر گازهایی است که میتوان به عنوان یک گاز ایدهال در نظر گرفت.
- ذرات کروی شکل و متشکل از یک ماتریس متخلخل همگن هستند.
- توزیع اندازه ذرات به صورت پراکنده است.
- اثرات نیروهای الکترواستاتیکی و تنش سطحی ناچیز در نظر گرفته میشوند.
- حرارت از دست رفته از طریق دیوار، ناچیز در نظر گرفته میشود.
توازن جرم، انرژی و مومنتوم برای یک حالت پایدار تکبعدی، برای فاز k و معادلات انتقال برای رطوبت جامد و گاز که از موازنه جرم کسر گردید، و در معادله زیر به آن اشاره گردیده است، در نظر گرفته شد. در این حالت، فاز k را میتوان هم فاز گاز (k=g) و هم فاز ذرات (k=p) در نظر گرفت.
موازنه جرم:
آنالوگهای چیلتون و کلبرن (معادله 16 مشاهده شود) برای محاسبه ضریب انتقال جرم استفاده میشوند.
همبستگیهای بایبس و دِبرانت ضریب انتقال را در فاز رقیق پیشبینی میکنند. در این مدل، اثر برخورد بین ذرات بر سرعت انتقال، با استفاده از همبستگی باندروسکی که در آن عدد ناسلت به عنوان تابعی از کسر حجمی جامد، ، است، بیان شد. این رابطه نشان میدهد که در بخش ورودی یک خشککن پنوماتیک، مقدار
، برای به تعادل رسیدن سرعت لغزشی بالا، دارای اهمیت است. به عبارت دیگر، این اثر با استفاده از تاثیر روی فاز پراکنده جامد در بخش ورودی ایجاد میشود.
9. نتایج و بحث
ابتدا، پیشبینیهای مدل با نتایج بدست آمده از اندازهگیریها توسط معادله بایانس بر روی یک خشککن پنوماتیک صنعتی مورد مقایسه قرار گرفت. سپس، در مرحله بعدی آنها با نتایج صنعتی اولیه بدست آمده در شرکت INEOS کلرووینیل مقایسه شدند.
در جدول 3، شبیهسازی دادهها، خواص PVC، پارامترهای ژئومتریک و فرایندی ارائه شده است.
1-9. مقایسه با یافتههای قبلی
در یک تحقیق صنعتی که توسط بایانس انجام شده، رطوبت PVC ورودی برابر با (0/26) و بزرگتر از رطوبت بحرانی (0/134) بود، بنابراین سرعت خشککردن توسط یک فرآیند دو مرحلهای کنترل گردید. مرحله اول تبخیر آبهای سطحی و مرحله دوم تبخیر آب درون حفرهها بود. در شکل 19، نتایج تئوری بدست آمده از پیوستگیهای مختلف ارائه شده در قسمتهای قبلی و همچنین اندازهگیریهای تجربی بدست آمده از بایانس در فرآیند صنعتی مشاهده میشود. در شکل 19، میزان رطوبت جامد در برابر طول لوله مشاهده میگردد، در حالی که در شکل 18 مقدار دمای هوا در برابر طول لوله به نمایش گذاشته شده است.
تفاوت بین داده های تجربی و یافتههای تئوری را میتوان به دلیل بدترین پراکندگی PVC منسجم در فاز گازی در منطقه ورودی لوله دانست. زمانی که دادههای تجربی با استفاده از پیوستگی باندروسکی بدست آمده باشند بیشترین تشابه را با یافتههای آزمایشگاهی دارا هستند. این امر را میتوان با استفاده از اثر سرعت لغزشی روی عدد رینولدز و سپس روی ضرایب انتقال جرم و گرما توضیح داد. این مقادیر در ورودی واقعا مهم هستند اما به تدریج در امتداد خشککن از اهمیت آنها کاسته میشود. این امر منجر به تغییرات بسیار مهمی در ضرایب انتقال میشود (شکل 21 مشاهده شود). در همبستگی باندروسکی Bandrowski این اثر توسط کسرحجمی جامدِ فاز پراکنده ضعیف است.
2-9. مقایسه با نتایج وینیلکلریدهای INEOS
برای ایجاد رطوبت و حرارت در طول پروفایل خشک کن پنوماتیک، خشک کن صنعتی INEOS به همراه چند رطوبتسنج و ترموکوپل مجهز شد. شکل 22، نشان دهنده مقایسه داده های صنعتی و نتایج عددی بدست آمده مورد استفاده در همبستگی باندروسکی است. میتوان اینگونه بیان کرد که مشخصات دمایی صحیح است، اما تفاوت های مشاهده شده در جریان خشک کردن به دلیل دیگر است: در خشک کن صنعتی، رطوبت در اولین متر ثابت است، اما در نتایج مدل، رطوبت به شدت افزایش مییابد. به دلیل پدیده پراکندگی (در مدل نادیده گرفته شد) سرعت در منطقه شتاب کاهش پیدا میکند.
3-9. بررسی پارامترها
نتایج حاصل از شبیهسازیهای زیر با استفاده از همبستگی باندروسکی و پارامترهای بایانس بدست آمد (جدول 3 مشاهده شود).
اثر جریان توده هوا خشک بین 25 و t/h46/4 مورد بررسی قرار گرفت. چنانچه در شکل 23 نشان داده شده است، این پارامتر تاثیر اندکی بر سرعت خشکشدن بالای t/h35 دارد. سرعت هوا تنها در منطقه شتاب بر نرخ خشککردن تاثیر دارد، پس از آن سرعت لغزشی با سرعت پایانی سقوط برابر میشود. در خروجی خشککن هوا اشباع نیست، بنابراین کاهش نرخ هوای خشک تاثیری بر برآیند نیروها نخواهد گذاشت (یعنی، کاهش نرخ هوا خشک از t/h46 به t/h35 سبب افزایش رطوبت جامد خروجی از 0/054 به PVCخشک kg/آبkg 0/067، و کاهش نرخ هوای خشک از t/h35 به t/h25 موجب افزایش رطوبت جامد خروجی از 0/067 به PVC خشک kg/ آبkg 0/097 میشود).
با توجه به آنچه که در شکل 24 مشاهده میشود، دمای ورودی یک اثر غالب دارد (یعنی افزایش در دمای ورودی از 96C به 156C سبب کاهش در حجم جامد خروجی از 0/097 به PVCخشک kg/ آب kg 0/014 میشود). در واقع، افزایش درجه حرارت اثر مهمتری بر نیروی محرکه انتقال حرارت دارد. اما از آنجایی که، رطوبت تعادلی وابسته به دما است، نیروی محرکه انتقال جرم نیز افزایش مییابد.
تاثیر رطوبت هوای ورودی بین 0 تا 0/0105 کیلوگرم آب/کیلوگرم هوایخشک مورد بررسی قرار گرفت. آخرین مقدار مربوط به اتمسفر هوای ( 15) که تقریباً اشباع است ( 98/4رطوبت نسبی)، بود. همانطور که در شکل 25 نشان داده شده، افزایش رطوبت هوای ورودی، موجب افزایش رطوبت جامد خروجی از 0/052 تا 0/054 کیلوگرم آب/ کیلوگرم PVCخشک شده است. این افزایش نشان میدهد که، رطوبت هوای ورودی که یک پارامتر ثابت است، کمی تحت تاثیر نیروی محرکه خشککردن میباشد. باید به این نکته توجه داشت که، دمای جامد خروجی متاثر است از:
- سرعت جریان هوای خشک در طول دوره سقوط سرعت خشک کردن به تنهایی،
- رطوبت هوا در طول دوره سرعت ثابت خشککردن به تنهایی و
- تاثیر آن بر دمای هوا در طول هر دو دوره.
در واقع میزان دما در مرحله سرعت ثابت خشک کردن به وسیله نیروهای محرکه خشک کردن کنترل میشود.
چنانچه در معادله 19 و 20 نشان داده شده، این نیرو فقط به رطوبت هوا و رطوبت تعادلی
که هر دو مستقیما به دمای جامد بستگی دارند، وابسته است. در مرحله سقوط سرعت خشک کردن، افزایش دمای جامد تا زمان رسیدن به تعادل گرمایی با هوا، ادامه می یابد، این تعادل توسط سرعت جریان هوای خشک و دما کنترل می گردد.
10. نتیجه
یک پروتکل تجربی و عددی برای مطالعه بر روی سنتیک خشک کردن مواد متخلخل در مقیاس ذرات مورد استفاده قرار گرفت. نتایج نشان از تاثیر قابل توجه پارامترهای عملیاتی خصوصاً دمای هوای و رطوبت داشتند. این نکته واضح است که خشککردن PVC توسط تقابل بین انتقالهای داخلی و خارجی کنترل میگردد. استفاده از یک نوع مدل کاهش ذره برای شبیهسازی خشککردن در سایز ذرات توسط دادههای تجربی مورد تایید قرار گرفت.
شکل (24). روند تغییرات دما و رطوبت جامد برحسب طول لوله برای دماهای مختلف ورودی: 96، 126 و 156C
PVC اساساً دارای ماکرومنفذ میباشد (nm250>dpore). کسر حجمی مزومنفذها (nm250>dpore>10) پایینتر از 10% است. به همین دلیل، ما مدل انقباض هسته را انتخاب کردیم، در این مدل میتوان ذرات را به صورت شبه کرههای همگن در نظر گرفت (یعنی، تخلخل و سایز یکنواخت در ذرات). در این مدل شبیهسازی صحیح سینتیک خشککردن صورت میگیرد. مغایرتهایی که در انتهای عملیات خشککردن مشاهده میشود، ممکن است مرتبط با انتقالهای صورت گرفته در مزومنفذها (ذرات اولیه) باشد.
یک مدل تکبعدی در حالت پایدار برای خشک کن پنوماتیک تعبیه گردید. این مدل برای فرآیند خشک کردن پودر PVC تر، مورد استفاده قرار گرفت. سرعت خشککردن در مرحله اول به وسیله انتقال هدایتی و در مرحله دوم توسط انتقالهای همرفتی و نفوذی کنترل گردید. مرحله اول، مرتبط با خشککردن آبهای سطحی شده و مرحله دوم مربوط به تبخیر آب در منافذ که به وسیله یک مدل انقباض هسته شبیهسازی شده، میشود.
در این مدل، انتقال هدایتی حرارت، جرم و مومنتوم لحاظ شده است. مطالعه پارامترها نشاندهنده این نکته است که دمای ورودی مهمترین پارامتر در فرآیند است. اما در این مدل پراکندگی پودر مرطوب که قطعاً گامی محدودکننده در فرآیند است، لحاظ نگردیده است.
* مترجم: سمیه صلاحی (مدیر کنترل کیفیت شرکت پارس پولیکا)
برای مشاهده اخبار شرکت پارس پولیکا اینجا را کلیک کنید.
نظرات